Phillips Industries jest światowym potentatem, który od 2016 roku ma fabrykę w Polsce. Jak należy produkować przewody i złącza, aby odnieść sukces na tak dużą skalę?
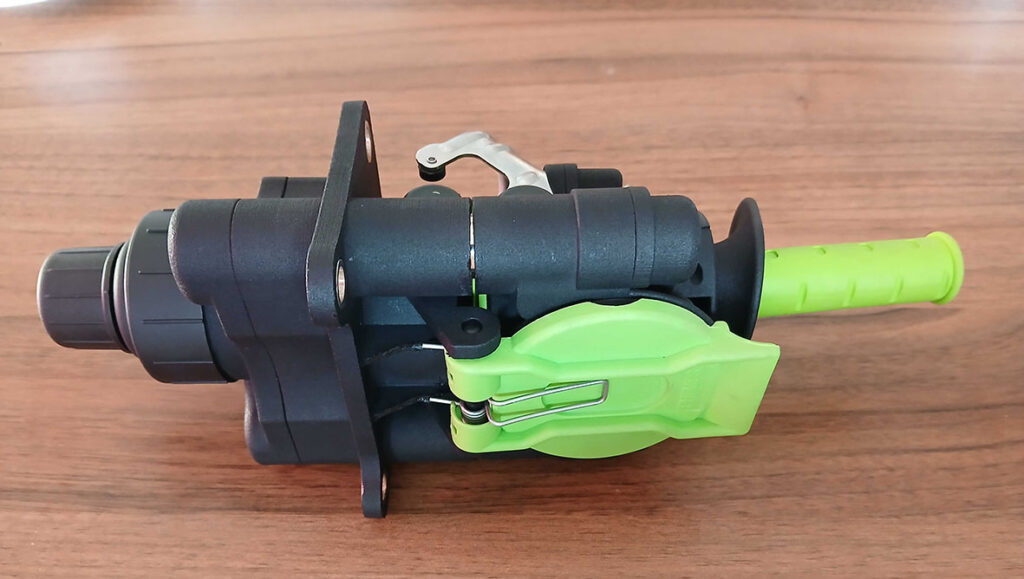
Od prawie 100 lat firma Phillips Industries pozostaje w rękach jednej rodziny i obecnie zarządza nią czwarta generacja Phillipsów. U steru firmy stoi Rob Phillips. A związany jest on z firmą od ćwierć wieku, a od 10 lat zasiada na stanowisku prezesa. To on dał silny impuls, żeby rozwijać markę Phillips Industries na świecie po zdominowaniu rodzimego rynku złącz elektrycznych i pneumatycznych. Obecnie Phillips dostarcza swoje produkty do 31 krajów i ma fabryki w Ameryce Północnej, Chinach oraz w Polsce.
Oddział Europa
W 2016 roku w Polsce zarejestrowano europejski oddział firmy Phillips Industries. Zakład produkcyjny powstał w Chechle koło Pabianic. Natomiast w halach o łącznej powierzchni ponad 7200 m2 zakład produkuje złącza elektryczne i pneumatyczne do pojazdów ciężarowych. Także wyroby plastikowe na wtryskarkach dla odbiorców zewnętrznych. 70% stanowią elementy złączy na własne potrzeby, a 30% to realizacja zleceń klientów, często spoza branży motoryzacyjnej. Wśród nich 90% stanowią wytwórcy AGD. W najstarszej części zakładu mieści się biuro projektowe, badawcze oraz narzędziownia przygotowująca matryce do wtryskarek. Odbywa się tu również produkcja i montaż podstawowego asortymentu zakładu, czyli przewodów łączących samochód ciężarowy z pojazdem ciągnionym.
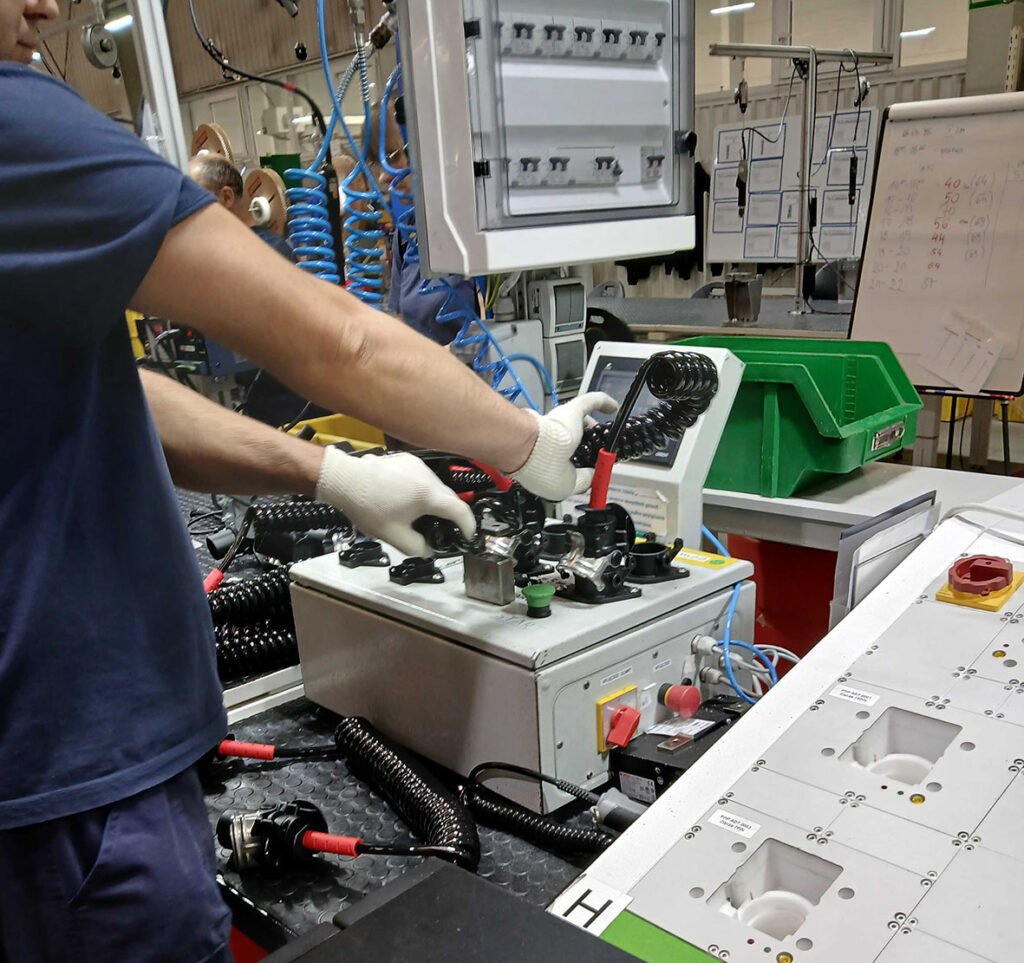
Większość elementów, z których składają się złącza, powstaje w hali produkcyjnej zakładu w Chechle. Dlatego tak ważne jest dogodne usytuowanie wszystkich działów odpowiedzialnych za badania, wdrożenie, kontrole procesów, przygotowanie oraz ciągłość produkcji. Własna narzędziownia pozwala nie tylko na wykonanie matryc, ale także ich szybkie naprawy i przeglądy. Nowe formy w narzędziowni w dużej mierze są zautomatyzowane. Natomiast projekt własny lub klienta zewnętrznego przesyłany jest z działu technicznego do programisty. Programuje on wtedy maszynę CNC, która wykonuje formę. Natomiast jeżeli trzeba dopracować jej kształt, robi się to ręcznie.
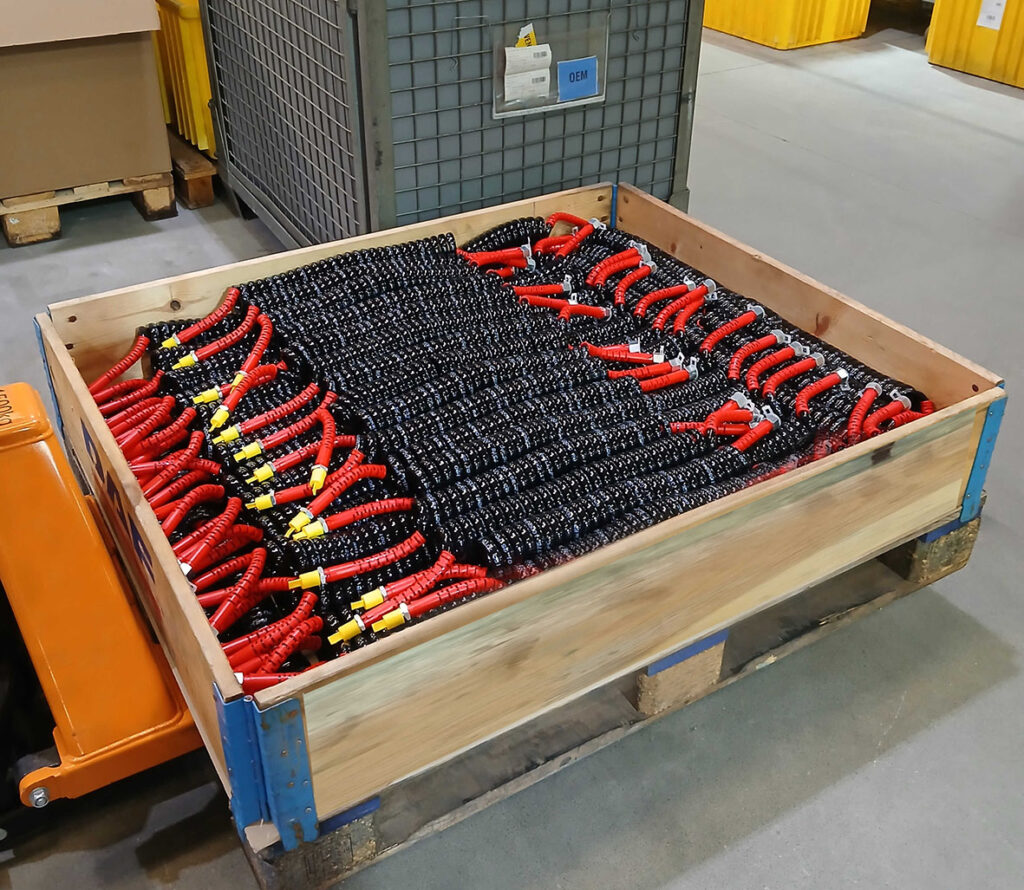
Skręcane i wygrzewane
Produkcja rozpoczyna się od przygotowania rur poliamidowych pod pneumatykę oraz kabli do złączy elektrycznych. Elementy te są poddawane spiralizacji i cięciu na odpowiednie długości. Potem zwinięte w spirale przewody wysyła się do pieców, gdzie natępuje wygrzewanie. Po kilkudziesięciu minutach kable wyciąga się i schładza, a na koniec przewija. Dzięki temu z większą siłą będą wracać do nadanego im spiralnego kształtu po rozciągnięciu.
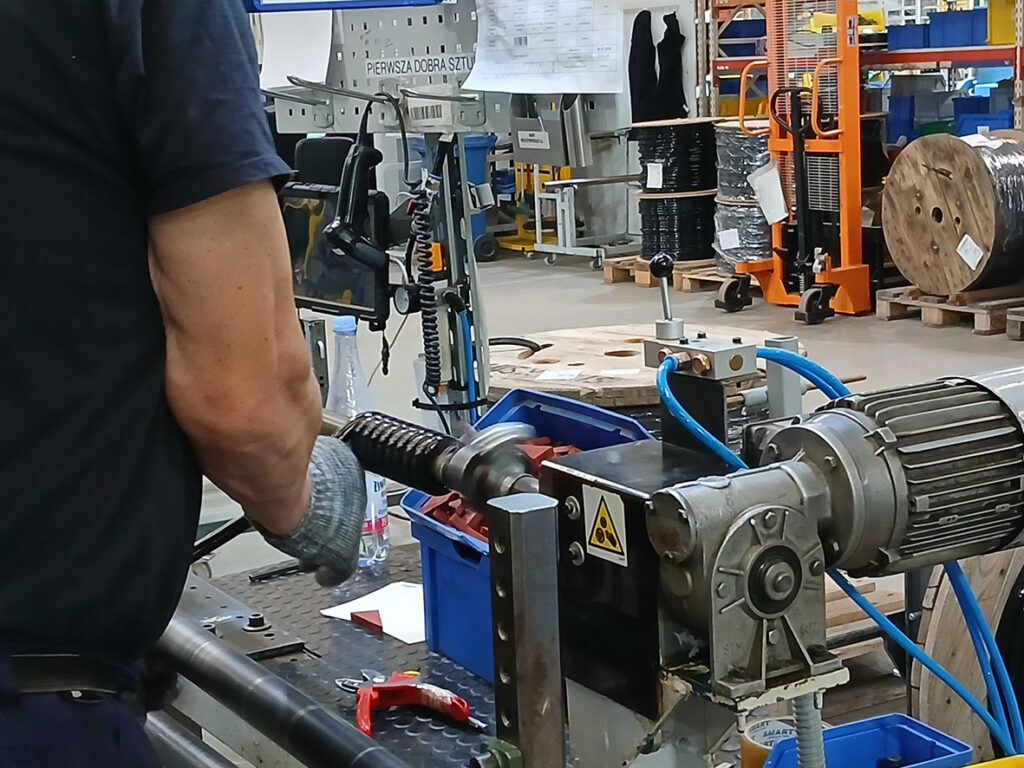
Przygotowane tak przewody wędrują na inne stanowiska, gdzie zakuwa się końcówki na wężach lub piny na przewodach. Przewody elektryczne uzbrojone w piny są wyposażane we wtyczki, do których na innym stanowisku przygotowuje się gniazda. Zakład produkuje złącza 12 i 24 V na 7 i 15 pinów, do podłączenia ABS i EBS oraz inne, włącznie z kablami rozruchowymi. Złącza elektryczne powstają aż w pięciu standardach. Podstawowy wyrób to Standard Solutions, który dostępny jest w wersji z elementami plastikowymi i aluminiowymi. Duracoil ma wzmocnione uszczelnienie oraz zwiększoną odporność na uszkodzenia… Czytaj dalej w magazynie fleetLOG 3/2025.